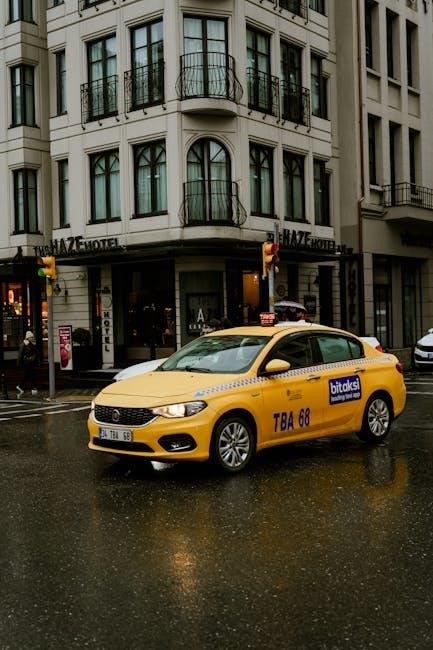
Electrical connections are essential for ensuring the safe and efficient flow of electricity in various systems. They involve joining conductors securely to maintain continuity and prevent hazards. Proper insulation and secure connections are critical for reliability and safety.
Definition and Importance of Electrical Connections
Electrical connections refer to the joining of conductors to ensure the continuous flow of electricity in a circuit. These connections are critical for maintaining safety, efficiency, and reliability in electrical systems. Properly executed connections prevent hazards like short circuits, overheating, and electrical fires. They are essential in residential, commercial, and industrial installations, ensuring that power is distributed evenly and securely. The integrity of electrical connections directly impacts the performance and longevity of electrical equipment. Without reliable connections, systems may fail, leading to downtime and potential risks. Therefore, understanding and implementing correct connection techniques is vital for any electrical installation. Different types of connections, such as splices and joints, are designed to meet specific requirements, ensuring durability and safety under various conditions. Regular inspection and maintenance of these connections are crucial to uphold their integrity and prevent failures.
Brief History of Electrical Connections
The history of electrical connections dates back to the early days of electricity, where the need for reliable conductor joints became apparent. As electrical systems evolved, so did the techniques for connecting wires and cables. Early connections were often crude, relying on twisting wires together or using simple soldering methods. However, these primitive techniques were prone to failures and posed significant safety risks.
Over time, advancements in materials and tools led to more secure and efficient connection methods. The development of standardized splicing techniques, such as the Western splice and the rat-tail splice, marked a significant improvement in electrical connections. These methods ensured better conductivity and durability, reducing the likelihood of electrical fires and system malfunctions.
In the 20th century, the introduction of insulation materials and modern soldering practices further enhanced the reliability of electrical connections. Today, electrical connections are a cornerstone of modern technology, enabling the safe and efficient distribution of power in homes, industries, and electronic devices. The continuous refinement of connection techniques underscores their critical role in advancing electrical systems.
Applications in Modern Electrical Systems
Electrical connections play a pivotal role in modern electrical systems, ensuring the reliable distribution of power across various applications. From residential wiring to industrial machinery, secure connections are essential for maintaining efficiency and safety. Different types of splices, such as the rat-tail splice and double twist splice, are commonly used in telecommunications, automotive systems, and home electrical installations.
In industrial settings, robust connections are critical for operating heavy machinery and ensuring uninterrupted production; Similarly, in renewable energy systems, such as solar panels, proper connections are vital for harnessing and distributing energy efficiently. Modern electrical connections also support advanced technologies like smart grids and IoT devices, enabling seamless communication and power distribution.
The applications of electrical connections extend to aerospace, medical equipment, and consumer electronics, where reliability and precision are paramount. Proper insulation and soldering techniques ensure that these connections withstand environmental stressors and maintain optimal performance over time.
Purpose of the Article
The purpose of this article is to provide a comprehensive guide on electrical connections, focusing on their types, applications, and best practices. It aims to educate readers on the importance of secure and efficient connections in ensuring electrical safety and system reliability.
By detailing various splicing techniques, such as the rat-tail splice and double twist splice, the article equips readers with practical knowledge for different scenarios. It also emphasizes the role of proper materials and tools in achieving durable connections.
The article serves as a reference for professionals and enthusiasts alike, offering insights into modern applications and safety considerations. Its goal is to promote understanding and adherence to best practices, ultimately enhancing the quality and reliability of electrical installations across various fields.
Types of Electrical Connections
Electrical connections include various splicing techniques such as the rat-tail splice, double twist splice, and T-junction splice, each designed for specific applications like extending cables or adding new lines safely and efficiently.
Prolongation Splice (Empalme de Prolongación)
The prolongation splice is a fundamental technique used to extend the length of an electrical cable or repair a cut wire. This method involves twisting the strands of two conductors together to ensure a secure and reliable connection. It is commonly employed in open installations and for conductors up to 4 mm². The simplicity of this splice makes it ideal for scenarios where cables are not subjected to movement or tension. Proper insulation is crucial to prevent electrical hazards, and the connection must be tightly secured to avoid any loose ends. This splice is widely used in applications such as telephone lines and overhead electrical wiring, where durability and safety are paramount. By following precise steps, the prolongation splice ensures minimal resistance and maximum conductivity, making it a essential skill for electricians and technicians.
Rat-Tail Splice (Empalme Cola de Rata)
The Rat-Tail Splice, also known as the twisted splice, is a simple and effective method for joining two electrical conductors. This technique is commonly used when the cables are not exposed to significant movement or tension, making it ideal for junction boxes, circuit assemblies, and other stationary applications. The process involves twisting the stripped ends of the wires together to create a secure connection. This splice is particularly useful in scenarios where space is limited, as it requires minimal room to execute. It is also a popular choice for DIY projects due to its straightforward nature. However, it is important to ensure that the connection is tightly twisted and properly insulated to prevent electrical hazards. While the Rat-Tail Splice is versatile, it is best suited for low-stress environments, as it may not withstand heavy mechanical strain. Proper execution and insulation are key to ensuring safety and reliability in this type of connection.
Double Twist Splice (Empalme de Doble Torsión)
The Double Twist Splice, or Empalme de Doble Torsión, is an advanced version of the standard twisted splice, offering enhanced mechanical strength and electrical integrity. This method involves twisting the conductors twice, creating a more robust connection compared to the single twist. The additional twist provides better resistance to stress and vibration, making it suitable for industrial applications where durability is crucial. This splice is particularly effective in environments where cables are exposed to mechanical strain or movement. The double twist ensures a secure bond, reducing the risk of connection failure over time. Proper insulation is still essential to prevent electrical hazards and ensure long-term reliability. While slightly more complex to execute than the Rat-Tail Splice, the Double Twist Splice offers superior performance in challenging conditions. It is widely recommended for installations requiring higher safety and durability standards, making it a preferred choice for professionals in demanding electrical environments.
T-Junction Splice (Empalme en T)
The T-Junction Splice, or Empalme en T, is a highly versatile electrical connection method used to branch power from one conductor to another, forming a “T” shape. This splice is particularly useful in applications where additional power sources or circuits need to be integrated into an existing electrical system. The process involves twisting one conductor over the other to create a secure junction, ensuring minimal electrical resistance and maximum safety. The T-Junction Splice is commonly employed in low-voltage installations, such as household wiring, and is favored for its simplicity and effectiveness. Proper insulation is crucial to prevent short circuits and ensure the longevity of the connection. This method is also ideal for temporary or experimental setups where flexibility is key. By providing a reliable and efficient way to branch electrical currents, the T-Junction Splice has become a fundamental technique in both residential and industrial wiring scenarios, offering ease of implementation and durability.
Materials and Tools Required
Essential materials include high-quality insulation tapes, soldering irons, flux, and heat-resistant sleeves. Tools like wire strippers, pliers, screwdrivers, and crimping tools are necessary for precise and secure electrical connections.
- Insulation materials for safety.
- Soldering equipment for reliable bonds.
- Wire strippers for preparing conductors;
- Pliers for twisting and gripping wires.
Insulation Materials for Safety
Insulation materials are critical for preventing electrical hazards and ensuring safe connections. Commonly used materials include PVC tapes, heat-resistant sleeves, and epoxy resins. These materials provide a protective barrier against short circuits, overheating, and environmental factors like moisture and dust.
Proper insulation ensures long-term durability and reliability of electrical systems. It also minimizes the risk of electrical shocks and fires. High-quality insulation tapes are designed to withstand various conditions, including temperature fluctuations and mechanical stress.
When selecting insulation materials, factors like voltage rating, flexibility, and adhesion must be considered. Applying multiple layers of insulation tape is often recommended to ensure complete coverage. Heat-shrink tubing is another popular option, offering superior protection against abrasion and chemicals.
Additionally, epoxy resins provide a strong and durable seal for connections exposed to harsh environments. Regular inspection of insulation materials is essential to maintain safety standards and prevent potential failures.
- PVC tapes for general-purpose insulation.
- Heat-resistant sleeves for high-temperature applications;
- Epoxy resins for durable sealing.
Soldering Equipment and Accessories
Soldering equipment is essential for creating reliable electrical connections. The primary tool is a soldering iron, available in types like temperature-controlled, adjustable, and butane-powered. Solder wire, typically rosin-core, is used to fuse conductors securely;
Accessories like soldering stands, heat-resistant sponges, and flux are crucial. A desoldering pump aids in removing excess solder, while tweezers help with precision work. Anti-static wrist straps prevent damage to sensitive components.
Additional tools include wire strippers for preparing cables and multimeters for testing connections. High-quality soldering equipment ensures safety, efficiency, and durability in electrical systems. Proper use and maintenance of these tools are vital for achieving professional results.
- Soldering iron for melting solder.
- Solder wire for bonding conductors.
- Flux to reduce oxidation.
Safety Considerations
Safety is crucial when handling electrical connections to prevent shocks and fires. Proper insulation, secure connections, and regular inspections are vital. Always use protective gear and follow guidelines to ensure safe and durable electrical systems.
General Safety Precautions in Handling Electricity
Handling electricity requires strict adherence to safety protocols to prevent accidents. Always de-energize circuits before working and verify voltage absence with a tester. Wear appropriate protective gear, including insulated gloves and safety glasses. Ensure work areas are dry and well-ventilated to minimize fire risks. Avoid overloading circuits and use tools rated for the task. Proper insulation of conductors is essential to prevent short circuits and shocks. Regularly inspect equipment for damage and replace worn components promptly. Never touch electrical components with wet hands or while standing on conductive surfaces. Keep flammable materials away from work areas. Training and knowledge of electrical systems are critical for safe practices. Adhering to these precautions ensures a safer environment for both professionals and end-users, reducing the risk of electrical hazards and promoting reliable connections.
Fire Risks and Prevention Measures
Electrical connections can pose fire risks if not properly installed or maintained. Poor insulation, loose connections, and overloaded circuits often lead to overheating, sparks, or arcing, which can ignite nearby flammable materials. To prevent fires, ensure all connections are secure and insulated with high-quality materials. Regularly inspect electrical systems for signs of wear, such as frayed wires or corroded terminals, and address issues promptly. Keep work areas clean and free from debris that could catch fire. Use surge protectors and circuit breakers to manage power surges and overloads. Proper ventilation in enclosed spaces is also crucial to prevent heat buildup. Adhering to international safety standards, such as those outlined in IEC or NFPA guidelines, further minimizes fire hazards. By implementing these measures, the risk of electrical fires can be significantly reduced, ensuring safer and more reliable connections.
Importance of Proper Insulation
Proper insulation is crucial for ensuring the safety and efficiency of electrical connections. It prevents the risk of short circuits, which can lead to electrical fires or equipment damage. Insulation materials, such as PVC or Teflon, protect conductors from environmental factors like moisture, temperature fluctuations, and physical stress. This protection extends the lifespan of electrical systems by reducing wear and tear. Additionally, insulation minimizes electromagnetic interference, ensuring signal integrity in communication and data transmission systems. In industrial settings, proper insulation helps maintain consistent power supply, reducing downtime and operational costs. Regular inspection and maintenance of insulation are essential to identify and address potential issues before they escalate. Without adequate insulation, electrical systems can become hazardous, leading to safety risks for people and equipment. Therefore, prioritizing insulation quality is vital for reliable and safe electrical connections in both residential and industrial applications.
Regular Maintenance of Connections
Regular maintenance of electrical connections is essential for ensuring their reliability and safety. Over time, connections can degrade due to environmental factors, wear, and tear, leading to potential hazards. Inspection of splices and joints should be conducted periodically to identify signs of damage, corrosion, or loose connections. Tightening screws and bolts is a simple yet critical step to prevent disconnections. Additionally, cleaning surfaces and applying lubricants where necessary can prevent oxidation and ensure smooth operation. Scheduled maintenance helps detect issues early, avoiding unexpected failures that could lead to downtime or safety risks. Proper tools, such as multimeters and thermometers, should be used to check for abnormalities in voltage, current, or temperature. Documentation of maintenance activities is also important for tracking the condition of connections over time. By prioritizing regular upkeep, electrical systems remain efficient, secure, and less prone to malfunctions, ensuring long-term performance and safety.
Best Practices for Implementing Electrical Connections
Best practices involve careful planning, precise execution, and thorough testing of connections. Proper insulation, secure fastening, and adherence to safety standards ensure reliability and efficiency in electrical systems, minimizing risks and enhancing performance.
Planning the Installation Carefully
Planning is crucial for a successful electrical installation. Begin by assessing the specific requirements of the project, including the type of conductors, load conditions, and environmental factors. Choose the appropriate splice type based on the application, such as empalme de prolongación for extending cables or empalme cola de rata for low-tension connections. Ensure all materials and tools are readily available and meet safety standards. Create a detailed schematic or diagram to guide the installation process, minimizing errors. Consider future maintenance needs and accessibility of connections. Proper planning ensures compliance with safety protocols, reduces risks, and optimizes system performance. Always refer to local electrical codes and manufacturer guidelines to guarantee reliability and efficiency. Adequate preparation prevents costly rework and enhances overall safety.
Executing the Splice Correctly
Executing the splice correctly is vital for ensuring the reliability and safety of electrical connections. Begin by preparing the conductors, stripping the insulation carefully to avoid damaging the wires. For empalme de prolongación, twist the wires firmly together, ensuring no loose strands remain. Apply soldering if required for added strength. For a Western splice, wrap the wires around each other in a specific pattern for enhanced mechanical strength. Once the splice is complete, insulate it thoroughly using high-quality materials to prevent short circuits. Regularly inspect the connection for signs of wear or damage. Proper execution ensures minimal resistance, reduces heat generation, and prevents electrical hazards. Always follow established techniques and safety guidelines to achieve a durable and secure connection. Correctly executed splices are essential for maintaining the integrity and efficiency of electrical systems. Proper methods prevent failures and ensure long-term reliability.
Testing the Connection for Safety
Testing the connection for safety is a critical step to ensure reliability and prevent hazards. Start by visually inspecting the splice for any loose strands, improper insulation, or signs of damage. Use a multimeter to check continuity, ensuring there is no unintended resistance between the connected wires. Verify that the connection does not introduce short circuits or open circuits. For empalme de prolongación or empalme cola de rata, test the strength by gently tugging on the wires to confirm they are securely joined. Apply a low voltage to the circuit and measure current flow to ensure it operates as expected. If soldering was used, inspect the joint for a smooth, even bond. Proper testing ensures the connection can handle the intended load without overheating or failing. Always disconnect power before testing and use appropriate safety equipment like gloves and insulated tools. Regular testing helps identify potential issues early, preventing electrical fires or equipment damage. Safety testing is non-negotiable for maintaining reliable and secure electrical systems.
Documentation and Record Keeping
Documentation and record keeping are vital for maintaining accountability and ensuring compliance with safety standards in electrical connections. Keep detailed records of each splice type, such as empalme de prolongación or empalme cola de rata, including materials used and testing results. Document the date, location, and purpose of each connection to facilitate future maintenance. Use standardized forms or digital tools to organize information, making it easily accessible for audits or troubleshooting. Maintain schematics and diagrams that illustrate the electrical layout, highlighting splice locations and configurations. Include photographs of completed connections for visual verification. Regularly update records to reflect any modifications or repairs. Proper documentation helps trace potential issues, reduces downtime, and ensures that all connections meet regulatory requirements. It also serves as a valuable resource for training new technicians and provides a historical record of system changes. Accurate and comprehensive documentation is essential for the long-term reliability and safety of electrical systems.
Electrical connections are fundamental for maintaining the continuity of electric current safely. Various types of splices, such as empalme de prolongación and cola de rata, are used to join conductors effectively. Proper materials like insulation and soldering tools ensure reliability. Safety measures, including insulation and regular maintenance, prevent hazards. Best practices involve careful planning, precise execution, and thorough testing of connections. Documentation and adherence to safety protocols are essential for long-term efficiency. Understanding these principles ensures secure and durable electrical systems.
Future Trends in Electrical Connections
Future trends in electrical connections emphasize advanced materials and smart technologies. Smart connectors and IoT-enabled systems will enable real-time monitoring and predictive maintenance. Automation in splice manufacturing will improve consistency and efficiency. High-temperature-resistant materials will enhance durability in extreme environments. Sustainable practices, such as recyclable insulation, will gain prominence. These innovations aim to increase safety, reduce maintenance costs, and support green energy integration.
Importance of Proper Techniques
Proper techniques in electrical connections are vital for safety, efficiency, and durability. Correct methods prevent risks like overheating, short circuits, and electric shocks. They ensure minimal resistance, reducing energy losses and enhancing system performance. Proper insulation and secure mechanical bonds are key to longevity. Skilled execution also lowers maintenance needs and extends equipment lifespan, ensuring reliable operation. Attention to detail and adherence to standards are essential for achieving these benefits.
Final Recommendations
Always prioritize proper techniques and materials when performing electrical connections to ensure safety and reliability. Use appropriate insulation materials to prevent fire hazards and maintain system integrity. Regularly inspect and maintain connections to avoid degradation over time. For complex installations, consult professionals to ensure compliance with safety standards. Adhere to best practices for splicing, such as using soldering equipment correctly and securing connections firmly. Proper documentation of electrical systems is essential for future maintenance and troubleshooting. Invest in high-quality tools and materials to guarantee durable and efficient connections. Finally, stay updated with the latest advancements in electrical connection technologies to improve system performance and safety.