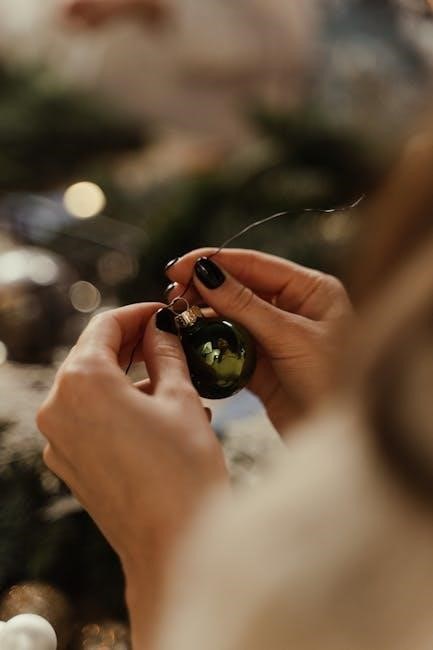
The Miller 70 Series Wire Feeder is a versatile, heavy-duty welding solution designed for industrial applications, offering precise wire feed control for MIG and flux-cored welding processes. Its durable construction and user-friendly interface make it ideal for high-volume production and fabrication. The manual provides essential setup, operation, and maintenance guidance to ensure optimal performance and safety.
1.1 Overview of the Miller 70 Series
The Miller 70 Series Wire Feeder is a high-performance, industrial-grade welding solution designed for MIG (GMAW) and flux-cored (FCAW) welding processes. Built for durability, it offers precise wire feed control and consistent performance in demanding environments. The series includes both single- and dual-wire feeder options, catering to various welding needs. Its robust design and advanced features make it ideal for heavy manufacturing, metal fabrication, and construction industries. The feeder is compatible with a wide range of welding wires, ensuring versatility for different applications. The Miller 70 Series is known for its reliability, ease of use, and adaptability to industrial production requirements.
1.2 Key Features of the Wire Feeder
The Miller 70 Series Wire Feeder boasts a range of advanced features, including a constant-speed wire feed system for precise control and consistent weld quality. It offers a wide wire feed speed range of 0.1 to 5.0 seconds, adaptable to various welding applications. The feeder supports both single and dual-wire configurations, enhancing versatility for different materials and thicknesses. Its robust design ensures durability in heavy-duty industrial environments, while the user-friendly interface simplifies parameter adjustments. Additionally, the feeder is compatible with a variety of welding processes, making it a versatile tool for metal fabrication, construction, and manufacturing industries. These features contribute to its reliability and efficiency in high-volume production settings.
1.3 Importance of the Manual for Operation
The manual is crucial for safe and effective operation of the Miller 70 Series Wire Feeder. It provides detailed instructions for setup, configuration, and maintenance, ensuring optimal performance and longevity. The manual outlines safety precautions, electrical requirements, and proper handling of welding wires to prevent accidents. Additionally, it offers troubleshooting guides for common issues, helping users resolve problems quickly and efficiently. By following the manual, operators can maximize the feeder’s capabilities, ensure consistent weld quality, and comply with industry standards. Regular reference to the manual is essential for maintaining the equipment and achieving the best results in industrial welding applications.
Technical Specifications of the Miller 70 Series Wire Feeder
The Miller 70 Series Wire Feeder features a wire feed speed of 50-780 inches per minute, supporting both MIG and flux-cored welding processes. It weighs 48 lbs (single-wire) or 87 lbs (dual-wire), designed for heavy-duty applications.
2.1 Wire Feed Speed Range
The Miller 70 Series Wire Feeder offers a wire feed speed range of 50 to 780 inches per minute (1.27 to 19.81 meters per minute). This broad range ensures precise control over various welding processes, from thin-gauge materials to thick industrial applications. The feeder’s speed setting is easily adjustable, allowing operators to optimize feed rates for different wire diameters and welding techniques. This versatility makes the Miller 70 Series suitable for both light fabrication and heavy-duty manufacturing environments, providing consistent and reliable wire feed performance across a wide range of welding applications.
2.2 Weight and Dimensions
The Miller 70 Series Wire Feeder is designed to be robust yet portable, with a weight of 48 lb (21.8 kg) for the single-wire feeder and 87 lb (39.5 kg) for the dual-wire feeder. Its compact dimensions ensure easy integration into various industrial settings, making it suitable for both stationary and mobile welding operations. The feeder’s durable construction and balanced weight distribution allow for smooth operation and reduced operator fatigue, even in demanding environments. These dimensions and weight specifications make the Miller 70 Series an ideal choice for heavy-duty manufacturing and fabrication applications while maintaining portability and ease of use.
2.3 Compatibility with Welding Processes
The Miller 70 Series Wire Feeder is compatible with a variety of welding processes, including MIG (GMAW) and Flux Cored (FCAW) welding. It supports both gas-shielded and self-shielded flux-cored welding, offering versatility for different industrial applications. The feeder’s design ensures seamless integration with these processes, providing consistent and reliable wire feed performance. This adaptability makes it suitable for a range of welding tasks, from light fabrication to heavy-duty manufacturing. The compatibility with multiple welding processes allows users to maximize productivity and efficiency across various projects, ensuring the Miller 70 Series remains a flexible and valuable tool in any welding environment.
2.4 Industrial Applications
The Miller 70 Series Wire Feeder is designed for demanding industrial environments, making it ideal for heavy manufacturing, metal fabrication, and construction projects. Its robust design and consistent wire feed performance ensure reliability in high-volume production settings. The feeder is also suitable for light manufacturing applications, offering versatility across various industries. With its ability to handle both MIG and flux-cored welding processes, the Miller 70 Series excels in applications requiring precise and durable welding solutions. Whether for large-scale fabrication or precise assembly work, this wire feeder is a reliable choice for meeting industrial welding demands efficiently and effectively.
Setting Up the Miller 70 Series Wire Feeder
The setup process involves initial installation, configuring wire feed speed, and selecting the appropriate wire type for optimal performance in various welding applications.
3.1 Initial Setup and Installation
The initial setup of the Miller 70 Series Wire Feeder involves mounting the unit securely, ensuring proper alignment with the welding machine. Connect the feeder to a compatible power source and verify all electrical connections. Install the appropriate wire type, threading it through the feeder’s drive system carefully. Calibrate the wire feed speed according to the manual’s guidelines to ensure consistent operation. Perform a test run to check for smooth wire delivery and adjust settings as needed. Proper installation ensures reliable performance and minimizes downtime during welding operations.
3.2 Configuring the Wire Feed Speed
Configuring the wire feed speed on the Miller 70 Series involves adjusting the digital interface to set the desired feed rate, ranging from 50-780 IPM (1.3-19.8 m/min). Access the menu, select the wire feed speed parameter, and use the adjustment buttons to achieve the precise setting. Ensure the display confirms the selected speed. Calibration may be required for accuracy. Proper configuration ensures consistent wire delivery, crucial for high-quality welds. Always refer to the manual for specific calibration procedures and guidelines tailored to your welding process and wire type. Accurate setup enhances productivity and weld performance.
3.3 Selecting the Right Wire Type
Selecting the appropriate wire type for the Miller 70 Series Wire Feeder is crucial for optimal welding performance. The feeder supports various wire diameters and types, including solid and flux-cored wires, designed for MIG (GMAW) and FCAW processes. Choose the wire type based on the specific welding application, material thickness, and desired weld characteristics. Ensure compatibility with the feeder’s feed roll and guide system. Proper wire selection enhances weld quality, reduces spatter, and minimizes the risk of wire feed issues. Always refer to the manual or manufacturer guidelines for recommendations on wire types and sizes for your specific welding tasks to achieve consistent results.
Operating the Miller 70 Series Wire Feeder
Operating the Miller 70 Series Wire Feeder involves starting the welding process, adjusting parameters like wire feed speed, and monitoring performance for consistent weld quality and efficiency.
4.1 Starting the Welding Process
Starting the welding process with the Miller 70 Series Wire Feeder involves ensuring the unit is properly set up and connected. Begin by powering on the feeder and selecting the appropriate wire feed speed for your application. Ensure the welding wire is correctly loaded and threaded through the feeder and torch. Perform a test run without arc to verify smooth wire feeding. Once ready, initiate the welding process by pulling the trigger on the welding torch, which activates the wire feed and starts the arc. Always wear proper safety gear, including a welding helmet, gloves, and protective clothing, before starting.
4.2 Adjusting Welding Parameters
Adjusting welding parameters on the Miller 70 Series Wire Feeder ensures optimal weld quality. Begin by accessing the control panel to set the wire feed speed, typically ranging from 50 to 780 IPM (1.3 to 19.8 m/min). Use the digital display to fine-tune settings for precise control. For MIG welding, adjust voltage and current based on wire diameter and material thickness. In synergic mode, the feeder automatically adjusts voltage to match the wire feed speed. Always refer to the manual for specific parameter ranges for different wire types and welding processes. Proper adjustment ensures consistent arc performance and high-quality welds across various applications.
4.3 Monitoring Welding Performance
Monitoring welding performance with the Miller 70 Series Wire Feeder involves observing the wire feed speed, arc stability, and weld quality. Use the digital display to track feed speed accuracy and ensure consistent arc performance. Regularly inspect the wire feed mechanism for proper alignment and tension to prevent irregular wire feeding. Listen for unusual noises or fluctuations in the welding arc, which may indicate issues like worn parts or incorrect settings. Adjust parameters as needed to maintain smooth operation. Proper monitoring ensures high-quality welds, reduces downtime, and extends the lifespan of the wire feeder. Always refer to the manual for troubleshooting guides.
Maintenance and Troubleshooting
Proper regular routine maintenance and prompt troubleshooting are crucial to ensure the optimal performance, reliability, efficiency, and longevity of the Miller 70 Series Wire Feeder.
5.1 Regular Maintenance Tips
Regular maintenance is essential to ensure the Miller 70 Series Wire Feeder operates efficiently and reliably. Clean the wire feeder and wire path frequently to prevent debris buildup. Lubricate moving parts periodically to maintain smooth operation. Inspect and replace worn or damaged components, such as drive rolls, to avoid wire feeding issues. Check the wire tension and adjust as needed for consistent feeding. Ensure all electrical connections are secure and free from corrosion. Refer to the manual for specific maintenance schedules and procedures to prolong the lifespan of the wire feeder and maintain optimal performance in industrial applications.
5.2 Common Issues and Solutions
Common issues with the Miller 70 Series Wire Feeder include wire slippage, inconsistent feed speed, and motor malfunction. For wire slippage, check and tighten the drive roll tension. If feed speed is inconsistent, ensure the wire is properly aligned and free from tangles. For motor issues, inspect for wear or debris and clean or replace parts as needed. Electrical connectivity problems can be resolved by checking and securing all connections. Refer to the manual for troubleshooting guides tailored to specific symptoms. Addressing these issues promptly ensures smooth operation and prevents downtime in industrial welding applications.
5.3 Replacement of Wear Parts
Regular replacement of wear parts, such as drive rolls and wire guides, is essential for maintaining the Miller 70 Series Wire Feeder’s performance. Over time, these components experience wear, leading to wire slippage or misfeeding. Inspect and replace the drive roll every 500 hours of operation or when visible wear is detected. Wire guides should be replaced if they show signs of damage or clogging. Use genuine Miller replacement parts to ensure compatibility and longevity. Refer to the manual for step-by-step instructions on disassembling and reinstalling these components. Timely replacement prevents downtime and ensures consistent welding results in industrial applications.
Safety Precautions
Ensure proper grounding of the wire feeder to prevent electrical shock. Always wear protective gear, including gloves and a welding helmet, to avoid injury from sparks or debris. Keep loose clothing tied back and avoid jewelry that could conduct electricity. Maintain a clean, well-ventilated workspace to prevent inhalation of welding fumes. Follow all safety guidelines outlined in the manual to minimize risks during operation and maintenance of the Miller 70 Series Wire Feeder.
6.1 General Safety Guidelines
Adhere to general safety guidelines when operating the Miller 70 Series Wire Feeder to ensure a safe working environment. Always wear appropriate personal protective equipment, including safety glasses, welding helmets with shaded lenses, gloves, and fire-resistant clothing. Keep the work area clean and free from flammable materials. Ensure proper ventilation to avoid inhaling welding fumes. Avoid wearing loose jewelry or clothing that could catch fire or get entangled in machinery. Follow the manufacturer’s instructions for installation, operation, and maintenance. Regularly inspect equipment for damage or wear and tear. Never operate the wire feeder near open flames or sparks.
6.2 Electrical Safety Measures
Ensure all electrical connections are secure and meet local codes when using the Miller 70 Series Wire Feeder. Avoid overloading circuits, as this can cause electrical hazards. Keep the wire feeder and power source away from water and moisture, as this can lead to electrical shock or equipment damage. Use properly rated fuses and circuit breakers. Never touch electrical components with wet hands or while standing on a wet surface. Regularly inspect all cables and connections for signs of wear or damage. If damage is found, immediately disconnect the power and have the unit repaired by a qualified technician.
6.3 Handling Welding Wires Safely
Always handle welding wires with care to prevent accidents and maintain weld quality. Store wires in a dry, clean environment to avoid rust or contamination. When loading or unloading wire, wear insulated gloves to protect against sharp edges or spools. Ensure the wire is properly secured to prevent tangling or whipping, which can cause injury. Regularly inspect the wire for signs of damage, such as kinks or fraying, and discard any compromised sections. Avoid touching the wire with bare hands, as oils from skin can affect weld quality. Properly dispose of wire scraps and packaging to maintain a safe working environment.
Accessories and Consumables
Explore essential accessories like drive rolls, contact tips, and shielding gas, designed to enhance performance and safety. Refer to the manual for consumables and ordering guidance.
7.1 Recommended Accessories
For optimal performance, the Miller 70 Series Wire Feeder supports various accessories, including drive rolls, contact tips, and shielding gas kits. These enhance wire feeding accuracy and weld quality. Additional accessories like nozzles, liners, and wire cutters are available to streamline workflows. A cooling system can be added for high-duty-cycle operations. Ensure all accessories are compatible with your specific wire feeder model for reliable operation. Refer to the manual for a detailed list of recommended products tailored to your welding needs.
7.2 Consumable Parts Overview
The Miller 70 Series Wire Feeder requires regular replacement of consumable parts to maintain optimal performance. Key consumables include drive rolls, contact tips, nozzles, and wire liners. These components wear over time and must be replaced to ensure consistent wire feeding and high-quality welds. Drive rolls are available in different sizes to accommodate various wire diameters, while contact tips and nozzles are designed to withstand high temperatures and wire abrasion. Refer to the manual for a detailed list of consumable parts and their replacement intervals. Genuine Miller parts are recommended to ensure compatibility and longevity of your wire feeder.
7.3 Ordering Replacement Parts
Ordering replacement parts for the Miller 70 Series Wire Feeder is streamlined through authorized distributors. Visit MillerWelds.com to locate your nearest distributor or contact the Miller Literature Department at 920-735-4356. Have your serial number ready to ensure accurate part identification. Printed manuals are available for $15, with shipping included. Genuine Miller parts are essential for maintaining performance and warranty validity. Use the detailed parts list in the manual to identify needed components. Online resources and customer support are also available to assist with orders and ensure timely delivery of replacement parts, minimizing downtime and keeping your operations running smoothly.
Warranty and Support
Miller offers comprehensive warranty coverage and dedicated customer support for the 70 Series Wire Feeder. Contact Miller at 1-800-4-A-Miller or visit www.MillerWelds.com for assistance; Manuals and resources are available online, ensuring uninterrupted support for optimal performance and troubleshooting.
8.1 Warranty Information
The Miller 70 Series Wire Feeder comes with a comprehensive warranty program designed to protect your investment. Miller Electric Mfg. LLC warrants this product against defects in material and workmanship for a period of one year from the date of original purchase. During this warranty period, Miller will repair or replace, free of charge, any defective parts. The warranty covers all components, including electrical and mechanical parts, ensuring reliable performance. For detailed warranty terms and conditions, refer to the official Miller 70 Series Wire Feeder manual or contact Miller’s customer service at 1-800-4-A-Miller.
8.2 Contacting Customer Support
For any inquiries, technical assistance, or support related to the Miller 70 Series Wire Feeder, customers can contact Miller Electric Mfg. LLC directly. The dedicated customer support team is available to provide troubleshooting, repair guidance, and general product information. You can reach Miller’s customer support by calling 1-800-4-A-Miller or by visiting their official website at www.MillerWelds.com. Additionally, support can be accessed through email or live chat on their website. Representatives are trained to address a wide range of concerns, ensuring prompt and effective solutions. For the most accurate and up-to-date contact information, refer to the product manual or the Miller Welds website.
8.3 Online Resources and Manuals
Miller Electric Mfg. LLC provides comprehensive online resources and downloadable manuals for the 70 Series Wire Feeder. Visit their official website at www.MillerWelds.com to access detailed product manuals, technical specifications, and troubleshooting guides. The website also offers instructional videos, FAQs, and software updates to support optimal use of the wire feeder. Additionally, printed copies of the manual can be ordered through the Miller Literature Department by calling 920-735-4356. For further assistance, customers can contact Miller’s customer support team, who are available to address any questions or concerns about the product. These resources ensure users have all the information needed for seamless operation and maintenance.
The Miller 70 Series Wire Feeder manual is a vital resource for optimizing welding operations, ensuring safety, and maintaining equipment performance for industrial applications.
9.1 Summary of Key Features
The Miller 70 Series Wire Feeder offers versatility for MIG and flux-cored welding, with precise wire feed control for consistent results. Its heavy-duty design supports industrial applications, making it ideal for high-volume production and fabrication. The feeder features adjustable speed settings, compatibility with various wire types, and a user-friendly interface for efficient operation. The included manual provides detailed guidance for setup, operation, and maintenance, ensuring optimal performance and safety. Designed for professionals, this feeder is a reliable choice for demanding welding tasks, combining durability with advanced functionality to meet the needs of industrial and manufacturing environments.
9.2 Final Tips for Optimal Use
For optimal performance, regularly clean and lubricate the wire feeder to prevent wear. Always use the recommended wire type and diameter for your specific welding needs. Store the feeder in a dry, cool place when not in use to avoid damage. Ensure a consistent power supply to maintain precise wire feed control. Follow all safety guidelines outlined in the manual to avoid accidents. Refer to the manual for troubleshooting common issues and performing routine maintenance. By adhering to these tips, you can extend the lifespan of your Miller 70 Series Wire Feeder and achieve consistent, high-quality welding results.